Safety: Protecting What Matters
We work to ensure a culture of safety first by empowering every employee to prioritize and actively participate in creating a safe workplace, from daily operations to executive oversight, with continuous improvement and comprehensive training.
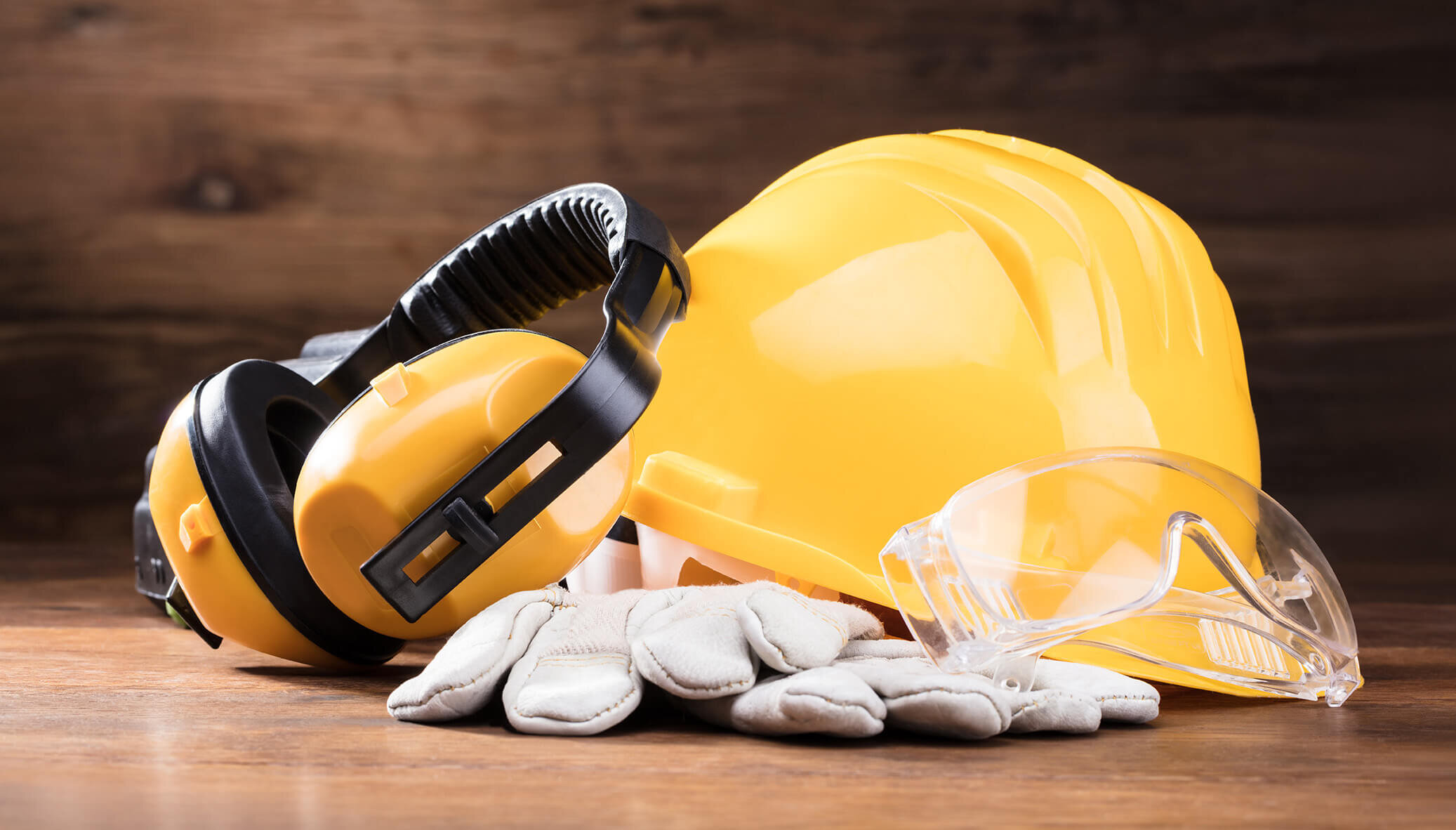
A Culture of Safety First
Safety is part of our culture, and we work diligently to continuously improve and maintain a safe workplace for our employees and our communities. Every employee is empowered with Stop Work Authority, giving them the ability and responsibility to stop a process or task at any time if it is viewed as unsafe or potentially harmful. The objective is to have all employees looking for safety improvements and opportunities. Our leaders and employees are responsible to every other employee to provide a safe work environment, so every team member returns home healthy and well every day.
Each manufacturing site starts their daily operations meetings with a safety discussion, related to learnings, incidents and our practices and processes. Weekly executive team meetings begin with a safety moment to discuss safety applicable situations to prompt the entire organization to focus on safety. Each quarter, an EHS (Environmental Health & Safety) Oversight Meeting is held between each manufacturing site leadership team and the EVP of Manufacturing, VP of EHS and Director of EHS to go over Safety, Environmental and Process Safety programs, progress of program improvements and support needs. In addition, annual short-term incentive compensation for each executive team member is tied to Environmental, Health and Safety (EHS) metrics. Our focus is, and must continue to be, to work with all leadership throughout the company to ensure that they are leading all employees to live by our “Protect What Matters” core value.
LSB’s EHS Risk Management Policy
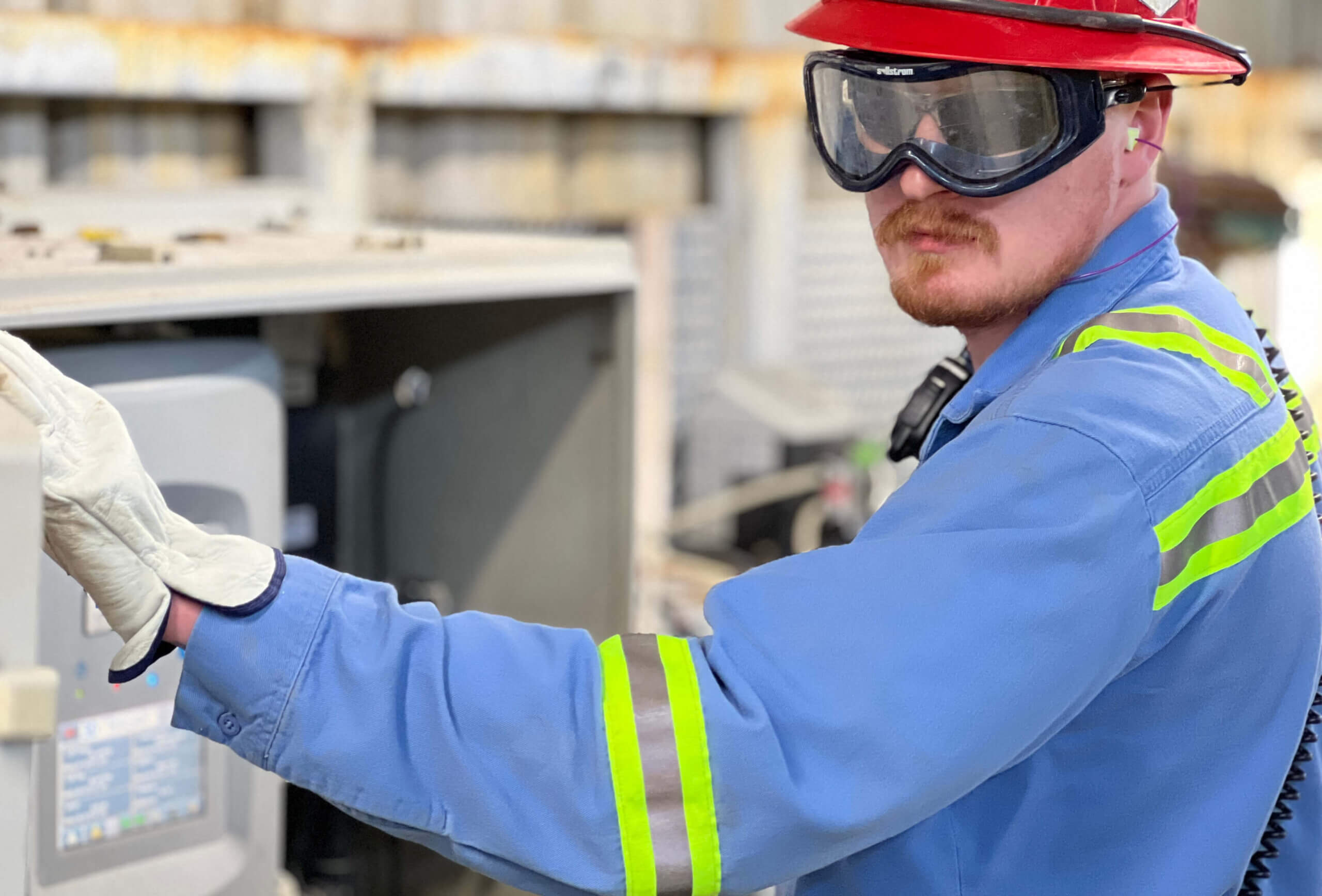
Goals
Workplace Safety
Our top focus is to promote safe practices in the workplace. Strong safety performance is the result of policies, processes, and procedures that help our employees remain injury free and succeed in their respective roles. We assess risk based on its highest consequence and we continue to implement measures to lower our recordable and lost time injury rates and raise safety awareness. Our goal is to create a culture that begins and ends with safety. The improvement of our safety performance is a journey requiring constant management, resources, and tools to support and equip our team.
Key Preventative Measures
- All manufacturing employees sign a “Commitment to Protect What Matters,” including a priority list of best practices and behaviors
- Hazard Recognition & Interaction program focused on pro-active actions and safety conversations
- Cross-site event, investigation and corrective action sharing with all sites for proactive prevention
- Empowered Safety Committees focused on improvement culture, processes and equipment
- Safety Scorecards for tracking metrics and focusing on trends
- WorkCare™ Injury Management Program
Safety & Process Safety Programs
As a chemical manufacturer of Ammonia, corrosives and oxidizers, we manage exposure risk through risk assessment, engineering controls, robust procedures, comprehensive Safe Work Permitting and Personal Protective Equipment (PPE). LSB believes in the value and results achieved through the disciplined execution of OSHA’s Process Safety Management program. We execute our PSM program fence to fence to ensure all operations are assessed through Process Hazard Analysis. Risk is further assessed with each change through our Management of Change program and with each job or task using our Job Safety Analysis process.

WorkCareTM Program
WorkCareTM is an occupational health and wellness services program we implemented to support the proactive management of employee injuries. The program provides us with access to trained medical advice in the first stage of an injury or discomfort, to evaluate the situation, provide self-care and first aid instructions, or make immediate recommendations to visit a health care professional. The goal is to manage injuries from the moment they occur, providing targeted care support and reducing the likelihood of more serious outcomes for our employees.